Hatch Smelter Optimizer maximizes throughput without changing existing processes, quality standards, or logistic restrictions downstream of furnaces.
It’s ideal for numerous smelting processes, including nickel, copper, and platinum group metals.
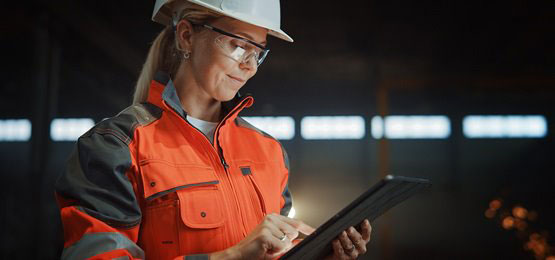
Navigate with certainty using Hatch Smelter Optimizer
Increase your throughput 11 to 15 percent: Powered by our no-code Hatch X Optimizer (HxO) software, the Hatch Smelter Optimizer helps customers unlock the full potential of the smelter by offering holistic planning and scheduling solutions.
Its features include:
“What-if?” Scenarios
Streamline converter cycles and optimize the quality and utilization of resources by conducting a comprehensive scenario analysis, thereby elevating overall efficiency and performance.
Evaluate key factors
Assess logistic, qualitative and energy factors to improve production rate and energy efficiency across the smelting process.
Process Debottlenecking
Optimize logistical operations in areas around smelting furnaces to improve throughput.
Energy Efficiency Improvement
Reduce overheating to improve energy efficiency; ensuring ladles are appropriately heated and ready for casters.
Time-Motion Analysis
Detailed time-motion analysis reports and dashboards improve movement efficiency along converter aisles.
Crane Schedule and Ladle Optimization
Reduce ladle tapping delays through efficient schedules and optimum ladle positions.
Interested in learning more?
Why Hatch Smelter Optimizer?
Hatch Smelter Optimizer maximizes the flow and production rates by taking into consideration all the processes, quality, and logistical constraints. This includes furnace bath levels and capacity, tapping rates, crane capacity and movement restrictions, and spatial restrictions for full/empty ladles at different processing stages. In addition to minute-to-minute or shift-to-shift production schedules, the model also incorporates two important practical features:
- Adjusting production schedules based on planned maintenance events
- Resource management leads to greater throughput and safety